Options & Upgrades
Programmable Drill Bank
Thanks to fixed bearing pre-load and rugged construction, Accu-Router spindles can plunge up to 600 in/min. But if your parts involve many holes, it’s hard to beat the price and performance of a vertical programmable drill.
Our standard configuration is 5 positions on 32mm centers, mounted adjacent to main routing spindle. Some customers sacrifice yield and mount a second spindle and drill either a fixed distance from the first combo, or with programmable servo-driven head spacing to reclaim some lost yield.
-
three spindles oriented to the X axis and three to the Y axis (in “L” formation, so actually five equally spaced spindles)
-
independently programmable spindles on 32 mm centers thru 48 additional work coordinate offsets supplied on CNC control
-
motor and starter supplied
-
very fast drillhead, popular with our user base
-
XR-15 routing spindle and drillhead are independently programmable – up or down on their retract slides
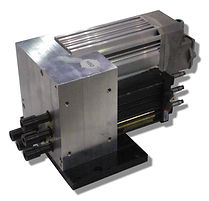
Auxiliary Flotation Tables
Don’t be too quick to discount our most popular and cost-effective workflow solution.
Also designed and fabricated by Accu-Router, these heavy-duty steel tables surround the main machine table at the same height, and are tied into your compressed air. In between part programs, flotation balls are pressurized for the operator to quickly and effortlessly unload spoilboard #1 (with cut parts and scrap).

Fixed or Variable Head Spacing
To increase productivity, some customers configure their Accu-Routers with (2) or more routing spindles and drill banks. We can review your programs and objectives to recommend the ideal setup for you.
-
Mounting spindles/drills on 24″ fixed center is popular in furniture
-
Multiple spindles can be manually adjustable with digital readout between programs (plywood reels etc)
An option worth considering is variable head spacing, sometimes called “servo lateral adjust”. Possible through a 4th axis in the host CNC control, spindle center distance can be altered by servo motor between cuts (common range 20-30″). Used in conjunction with popular CAM software like SigmaNEST and Plataine, this can reclaim up to 10% of the yield lost with multi-head machining, paying for itself quickly in better material utilization.
Accu-Setter Touch Block
Accu-Router is pleased to announce another productivity enhancement for Accu-Router CNC routers: introducing the Accu-Setter automatic tool setter. This rugged, highly accurate and repeatable device assists the operator in setting the critical tool depth-of-cut. Tooling depth is an often incorrectly set parameter in the control, resulting in broken tooling, premature spoilboard and tool wear, incorrect parts, or worse, spindle crashes.
The Accu-Setter sits directly on top of the spoil-board in a dedicated spot, secured by a pin on the side of the router table to assure proper placement. A simple M-Code is executed, and the router does the rest. Z depths are set according to the offset that is being used for programming. In the case of machines with automatic tool changers, the offset is applied according to the tool that is in the spindle. When not in use, the Accu-Setter resides in a designated holder with a proximity switch that senses the block and will not allow the router to operate; assuring that the Accu-Setter is in the proper place to avoid damage by the machine. As with most of Accu-Router enhancements, the Accu-Setter is readily available for most Accu-Router machines.

Fanuc CNC
GE Fanuc controls have also been the gold standard since 1972 — the name literally means Fuji Automatic Numerical Control. Uptime, reliability, residual value – none better. Like your home computer, components in PC based controls are prone to obsolescence and failure after only a few years. Fanuc controls on 30 year-old Accu-Routers are still going strong. Why use anything else? There’s a pattern forming — to save up-front cost.
And don’t assume for a second that all Fanuc controls are created equal. One furniture customer reports their Accu-Routers process 25 more nested panels/shift than equivalent Fanuc competition. How? Years of optimizing & tuning settings of Fanuc controls for maximum performance. It’s about precise acceleration & deceleration (ACC/DEC), AI Contour Control (AICC), looking ahead in the program and expediting upcoming moves within acceptable tolerance.
Our Green CNC program uniquely leverages the stability and longevity of Fanuc controls — in this case, models a generation or two old on platforms re-acquired for modernization. While a 1990’s Fanuc control may lack the latest bells & whistles — ethernet/flash datacom, ultra-precise high-speed cornering — it’s still vastly superior to off-brand or PC-based units. Dozens of Accu-Router customers have opted for the savings of a pre-owned 18M control, which are also compatible with most nesting/CAM software.
No matter the cost, you do owe it to yourself to fully consider Fanuc’s latest control technology. Like the engine in a high-performance automobile, it’s what really unleashes a High Velocity Accu-Router. Below is a description of our current flagship, the Model 0i-MF.
This control comes standard with many high speed features so important to cell productivity:
-
automatic cornering software for maximum cornering speeds,
-
advanced look ahead capability,
-
10.4” LED color monitor,
-
Ethernet & PCMCIA high density memory card plug-in slot
-
high response Fanuc servo motor technology,
-
custom Macro, programmable data input,
-
work piece coordinate offset, 48 extra offsets,
-
Bell Shape ACC/DEC high speed machining
-
Alpha Series servos: up to 50% energy savings via faster cycles, power source regeneration
On its predecessor flagship 18i-MB, AICC/HPCC and bell shape ACC/DEC were combined $5,300 upgrade – now available at no additional cost! If your Fanuc CNC control is five years or older, this new control technology will likely be cost justifiable for an upgrade or retrofit.
Fanuc CNC controls are more value laden than ever before. Block processing speeds and closed loop feedback are accomplished at rates much faster than in the past. The end result is the ability to achieve machine motion and machining rates as much as five times faster than older CNC machines. Automatic cornering speeds can reduce cycle times up to 30%, especially in programs with multiple radii moves.
Accu-Router’s Green CNC remanufacturing program upgrades older Accu-Routers with new mechanical components so that a Fanuc control retrofit can truly result in dramatic improvement in output. A Fanuc CNC control retrofit does involve all new machine electronics, servo motors, cables, control components, etc, which are housed in reconditioned NEMA-12 (dust tight) enclosures – passing back more savings to the customer.
Every Accu-Router customer receives personalized CNC control ladder architecture developed exclusively for their application requirements. This exclusive attention maximizes productivity, safety, and operator communications, and can be modified upon customer request at any point in the future. This also allows for complete integration of any peripheral devices through the host CNC control, such as an automated conveyor system, perimeter guarding, etc. This level of customer interface is simply not offered competitively – JUST ASK OUR CUSTOMERS!
Click the picture below to learn about the latest Fanuc model, the 0i-MF Plus.
Accu-Sweeper
Even the most advanced CNC routers have spoil boards or carrier panels that accumulate dust during machining. Cleaning those panels slows down production and occupies the operator with important housekeeping duties.
Enter the ACCU-SWEEPER, an integrated air purge and baffled hood system that interfaces to your dust collector, ideally straddling our custom-fabricated flotation workflow tables (sold separately).
After removing cut parts, just push your carrier panel under the baffled hood where it’s swept clean by the integrated air purge system and suction from your dust collector. Achieve even greater performance with mechanized through panel feeder (optional).
The ACCU-SWEEPER will keep your work area cleaner and make your operator more productive. 4’, 5’ and custom sizes available.
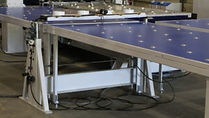
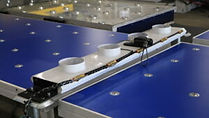
Nesting / CAM Software
So many CNC parts originate as Computer Aided Drafting (CAD) files, which can then be converted to numeric code and toolpaths required by machine tools.
Nesting, CAM and production scheduling software can greatly accelerate the payback and efficiency of a CNC install. Every Accu-Router has its own “post processor” to communicate with your internal systems. We work seamlessly with a wide-range of packages, many of which now offer monthly subscription models. In alphabetical order:
CATIA
(popular in aerospace, automotive)
CATIA goes far beyond traditional 3D CAD software tools to offer a unique Digital Product Experience, based on the 3DEXPERIENCE platform. Sustainable development is driving companies around the globe to create a constant stream of innovative and inspiring smart products. Engineering, Design, Systems Architecture and Systems Engineering of these products becomes more demanding.
Mastercam
Mastercam gives your shop the best possible foundation for fast and efficient router cutting. From general purpose methods such as optimized pocketing to highly specialized toolpaths like 5-axis trimming. Mastercam ensures that you’re ready for any job. Mastercam delivers:
-
Full 3D CAD modeling.
-
Easy pocketing, contouring and drilling.
-
Built-in nesting, engraving, aggregate tools and much more.
-
Streamlined multi-axis cutting, trimming, and drilling.
-
Optimized motion boosts tool life and decreases cutting time.
-
Specialized options for focused projects.
Router-CIM
Router-CIM ® 2014 Automation Suite is a complete CNC machine programming package. This versatile product combines Computer Aided Manufacturing (CAM) features with the power of AutoCAD®, the world’s premiere Computer Aided Design (CAD) software. Router-CIM® 2014 can not only run inside the latest version of AutoCAD ®, it is also compatible with AutoCAD ® 2014, 2013 and 2012. Includes 64 bit support.
Plataine
Plataine’s Total Production Optimization (TPO) software solutions bridge the gap between Customer, Manufacturing and Engineering requirements. TPO integrates data from the ERP’s order management and inventory warehouse modules, CAD software, and production-floor systems to automatically create optimized production plans. Plataine’s patent pending technology is used by FDM 300’s top upholstery manufacturers.
SigmaNEST
SigmaNEST offers an advanced nesting solution that optimizes the technology of a CNC router with high-efficiency nesting, superior part quality, and significant control of standard router cutting functions.
As the leading router software for nesting and programming single or multi-spindle wood and metal CNC routing machines, SigmaNEST is ideal for high-efficiency production in frame shops, boat and furniture manufacturers.
Safety & Guarding
Perimeter Guarding
All existing Accu-Router machines can be fitted with a 6′ tall cyclone fence bolted to the floor which goes around the back half of the machine. There are two 3′ wide doors that open to a 6′ wide opening in the back of the machine that gives access for service or maintenance requirements. The front of the machine can be guarded with 3′ wide unitized pressure mats that can be placed around the front and along both sides of the machine. This custom design provides for full perimeter protection and will not restrict machine access or hinder productivity. Our solution is also shop friendly in terms of environmental considerations. A custom system can be made to fit your requirements. In addition, light curtains and safety scanners are available.
Safety Labeling
Whether all new or re-built, all Accu-Routers that pass through our factory receive the latest high-visibility, ANSI-compliant, safety labeling.
Stack Light
An optional stack light can be placed on top of the main operator control cabinet. When the machine is cutting the light is green. When the machine is sitting idle for less than one minute (time can be adjusted), the light is yellow. When the machine is idle for more than one minute, the light turns red. The stack light is used as an operator accountability measure. It helps maintain and recognize the importance of constant running time on the routers. This is especially effective with multiple routers in place.
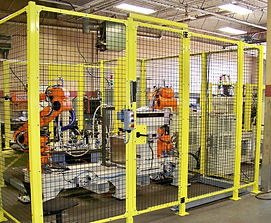
